1. 서 론
2. 본 론
2.1 로터디스크 구동부
2.2 시편 위치 제어부
2.3 버너시스템
2.4 제어/DAS 시스템
3. 열전달 해석 및 검증시험 결과
3.1 내마찰 시험장치 열전달 해석결과
3.2 내마찰 시험장치 검증 결과
4. 결 론
1. 서 론
항공용 가스터빈 엔진은 고성능, 고효율화를 목표로 지속적으로 각 구성품, 소재 등에 관한 주요 핵심기술의 연구 개발이 진행 중에 있으며, 최적의 사이클 성능을 갖는 엔진 개념부터 구성품의 성능, 효율 향상과 운용 온도의 증가를 위한 냉각 기술 및 소재 개발에 관한 다양한 기술들이 연구되고, 실 엔진에 적용되어 왔다[1].
엔진의 성능이 향상됨에 따라 1970~80년대에는 고온에 노출되는 금속 소재의 열적인 안정성을 확보하기 위해 단결정의 합금소재 개발과 냉각효율을 상승시키기 위해 기술개발을 하였는데, 운용 온도의 상승과 함께 금속소재의 온도 한계인 1,100℃를 넘는 조건에서 엔진을 운용하게 되어 Fig. 1과 같이 금속 소재의 운용 안정성을 위한 열차폐 코팅 연구가 1980년대부터 진행되어 오고 있다. 실제 미국 GE(General Electric) Aviation, 유럽의 Eurojet 등 해외 선진 엔진 제조사에서는 터빈입구온도(Turbine Inlet Temperature, 이하 TIT) 1,800 K에서 운용할 수 있는 엔진을 보유하고 있으며, 현재 TIT 1,900 ~ 2,000 K급 엔진 개발을 수행 중에 있고 고압터빈부에 해당하는 구성품에 대한 열차폐 코팅연구가 수행되고 있음을 확인한 바 있다.
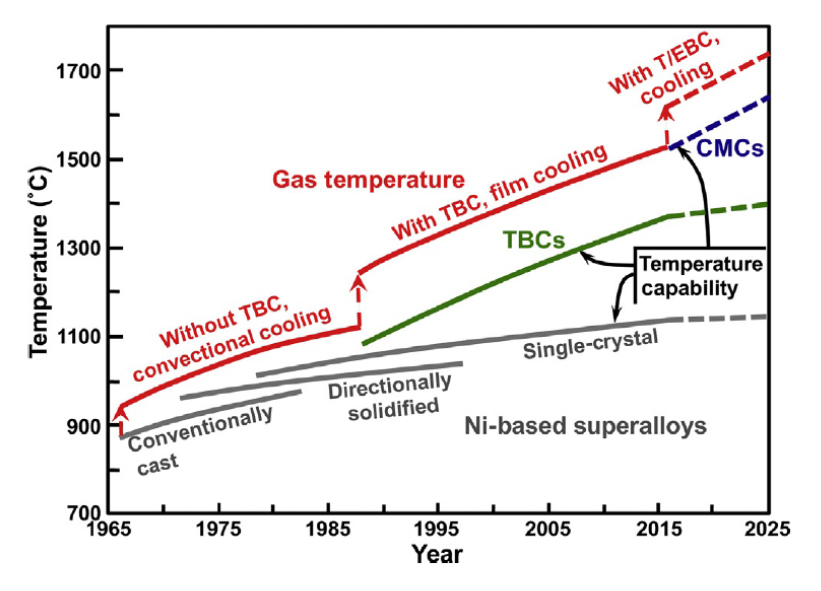
Fig. 1
Historical data of maximum gas inlet and material surface temperature with and without thermal barrier & cooling[2].
국내 독자 터보팬 엔진개발에서도 기존의 개념설계 수준에서 달성하였던 터빈입구 온도 1,350 K 및 1,600 K급보다 높은 1,800 K급의 엔진 개발을 목표로 하고 있으나, 코팅공정 기술 및 시험평가에 관한 기술 등에 대한 기술보호로 관련 기술의 해외도입도 제한을 받고 있어 이에 대한 많은 연구가 필요한 상황이다.
또한 엔진의 고효율화를 위한 다양한 접근이 있었으며, 그중 고압터빈부의 슈라우드와 블레이드 팁 간극사이에 발생하는 누설유동(Bypass leakage)에 의한 손실을 최소화하기 위해 엔진 운용 구간에서 간극제어를 위한 케이싱 냉각기술을 적용하였는데, 최근에는 Fig. 2와 같이 블레이드 팁에 의한 슈라우드 면의 의도적인 마모를 통해 간극을 최적화하면서 동시에 열차폐 성능을 보유한 마모성 세라믹코팅(Abradable ceramic coat -ing)에 관한 연구도 진행되고 있다[3,4].
Fig. 3은 고압터빈에서 블레이드 팁(Rotor)과 슈라우드(Stator)사이 간극에 관해 Take-off, Climb 그리고 Cruise 상황에서 슈라우드 케이스 냉각의 유무에 따라 간극이 어떻게 변화하는지를 보여준다. 이 블레이드 팁과 슈라우드 사이의 간극은 과도할 경우 블레이드 팁에서 발생한 유동과 그에 따른 Vortex 패턴으로 인해 사이클 효율의 손실 및 유동의 불안정성을 유발할 수 있으며, 불충분한 경우 냉각 유동을 제한하며 표면 마찰, 과열 발생으로 구성품의 수명을 단축할 수 있으므로 적절한 간극 제어가 필요하다[4]. 이때 마모성 코팅(Abradable coating)을 적용하여 Top 코팅층을 블레이드 팁에 의한 컷팅 희생층(Sacrificial seal)으로 제공해 마모에 의한 적정 간극 제어를 할 수 있게 한다.
또한 지난 수십 년간의 연구를 통해 간극을 최적화할수록 경제적인 측면에 이점이 있음을 확인하였는데 Steinetz(2004)는 고압터빈(HPT)의 팁 간극이 25 μm 감소하면 연료 소비율(SFC)이 0.1% 낮아져 미항공사에서 매년 2천만 갤런의 연료를 절약할 수 있다고 하였으며, 이러한 사례들을 통해 Wilson, S.(2012)는 간극과 누설에 따른 효율 변화에 대해 선형적인 관계를 가정할 경우 50% 간극 감소는 약 2%의 효율 상승을 가져올 수 있음을 언급하였다[5].
본 논문에서는 TIT 1,800 K급 이상 엔진의 고효율화를 위한 터빈 슈라우드의 마모성 세라믹코팅의 최적화 기술 확보를 위해 코팅 설계 및 공정 변수에 따른 마모 특성을 평가하기 위한 고온 내마찰 시험 장치(High Temperature Abradabil -ity Test Stand)를 설계하였으며, 실제 제작 및 성능 시험을 통해 장치의 적절성을 확인코자 하였다.
2. 본 론
가스터빈 엔진의 블레이드에 의한 슈라우드 코팅면 마모를 모사하기 위한 내마찰 시험장치는 커팅 블레이드를 장착한 로터디스크 구동부와 코팅 시편을 장착하여 엔진 운용 간 발생 가능한 블레이드 팁의 침입속도(Incursion rate)와 깊이(Incursion Depth)를 제어하는 시편 위치 제어부, 코팅시편이 TIT 1,800 K 조건에서 슈라우드 코팅면 온도[4]인 1,100 ~ 1,150℃을 유지할 수 있도록 한 버너시스템과 이를 제어하기 위한 제어/DAS시스템으로 나누어 설계, 제작하였다.
2.1 로터디스크 구동부
로터디스크 구동부는 시험베드 위에 모터 지지부와 전후방 로터조립체/지지부에 의해 고정되며, 로터디스크는 퀼 샤프트로 구동모터와 연결하여 회전 동력을 전달하도록 하였다.
로터디스크는 Fig. 4와 같이 5,500 lbf급 가스터빈 엔진에 적용하였던 실 형상을 적용하였으며, 내마찰 시험을 위한 커팅 블레이드(Cutting blade)와 회전 균형을 위해 밸런싱 블레이드(Balancing blade)를 180° 간격으로 Fig. 5와 같이 한 개씩 장착하였다. 또한 운용 중 고속 회전에 의한 동력손실과 소음을 최소화하기 위해 퍼트리 구조를 가진 블랭크(Blank)를 로터 디스크에 장착할 수 있도록 설계하였다.
로터디스크를 고정하기 위한 샤프트는 디스크와 같이 블레이드 팁 속도 기준 최대 450 m/s로 고속회전을 하기 때문에 좌ㆍ우 샤프트는 그리스 윤활 방식의 Angular 볼베어링을 2개씩 적용하여 지지하였다. 최대 속도까지 운용됨에 있어 안정성을 확인하기 위해 Fig. 6과 같이 동특성 해석을 수행하였으며, 로터디스크와 사프트를 포함한 회전체의 1차 위험속도는 최대 운용속도 대비 65% 이상의 마진(Margin)으로 충분히 높게 설계되었다. 이를 통해 회전체의 과진동 및 이상 진동을 회피하고, 동특성의 영향을 최소화하여 내마찰 시험을 안정적으로 수행할 수 있게 하였다.
로터디스크 구동부 지지시스템은 모터를 고정하는 지지부와 로터디스크 샤프트를 지지하는 전후방 지지부로 구성하였다. 위험속도를 충분히 높여 동특성의 영향을 최소화할 수 있도록 회전체의 회전관성을 고려한 지지부의 충분한 강성이 요구되어 강건 지지로 설계하였다. 로터디스크 샤프트를 지지하는 전후방 지지부에는 볼베어링을 2개씩 장착하였으며, 운용 간 발생할 수 있는 마찰열을 냉각할 수 있도록 베어링 냉각 공압 라인을 설계하였다.
동력 전달축은 Fig. 7과 같이 양쪽이 스플라인 형상인 Quill shaft로 설계하였으며, 모터와 로터디스크 샤프트를 연결하여 회전력을 전달하도록 하였다. 내마찰 마모시험 중에 비정상적인 마찰에 의한 부하 증가시 모터에 과부하가 발생하지 않도록 Quill shaft의 사이징을 결정하였으며, 구동부와 피동부 사이의 간격을 최소화하도록 설계하였다.
구동 모터의 형식은 영구자석동기모터(PMSM, Permanent Magnet Synchronous Motor)로서, 300VAC, 최대 120kW 출력 성능을 보유하고 있으며, 독립형 블로워를 통해 모터 내부를 냉각하도록 설계하였다. 모터의 최대 회전속도는 로터디스크의 커팅블레이드 팁 속도 기준 최대 450 m/s를 만족할 수 있도록 하였다.
2.2 시편 위치 제어부
시편 위치 제어부는 크게 시편 홀더부와 시편 위치 구동 시스템으로 구성되어 있으며, 시험시편을 장착한 상태에서 회전하는 커팅 블레이드에 일정한 속도와 깊이를 제어할 수 있도록 설계되었다.
시편 홀더부는 Fig. 8과 같이 가로, 세로 길이 100 mm × 50 mm 시험 시편을 클램프로 고정하여 커팅 블레이드와 마찰 충돌 시 시편이 흔들리지 않도록 설계하였으며, 버너 시스템을 통해 시편에 가해지는 고온 화염에서 시편 홀더부의 손상을 방지하기 위해 화염 노출부위에 세라믹 열차폐코팅을 하였다.
시편 위치 구동 시스템은 Sporer, D.(2007)가 제시한 기본 형상[6]을 참고하였으며, Fig. 9와 같이 시편 홀더부, 시편 홀더부 냉각판(Cooling plate), 스텝모터, Linear Guide로 구성하였다. 시편 제어부에는 코팅 시편의 후면온도를 측정하기 위한 온도센서와 커팅 블레이드 충돌 마찰시 충격량을 측정하기 위한 힘센서 그리고 침입량(Incursion depth)을 제어할 수 있도록 Depth senor를 장착하였다. 냉각판(Cooling plate)은 내마찰 시험 중에 시편 제어부를 고온으로부터 보호하기 위해 내부에 냉각유로를 설계하여 수냉식으로 제어하였다. 그리고 PLC 방식으로 제어되는 스텝모터(Step motor)와 리니어 가이드(LM Guide)를 적용하여 침입율(Incursion rate)을 5 ~ 1000㎛/s에서 5㎛/s 정밀도를 구현하였다.
2.3 버너시스템
버너시스템은 크게 압축공기시스템, 연소식 버너, 연료(프로판 가스) 및 공급라인으로 구성되며, 내마찰 시험장치의 시험 시편의 표면온도를 약 1,100 ~ 1,150℃로 가열할 수 있는 화염을 분사할 수 있도록 설계 하였다. 연소식 버너는 토치형 버너와 달리 제트 유속을 만들어 실제 가스터빈 엔진 터빈부의 고온 환경을 모사할 수 있도록 하였으며, Fig. 10의 NASA의 GRC Mach 0.3 Burner rig를 참고하여 설계 및 제작하였다[7].
연소식 가스버너는 연료(프로판 가스)와 압축공기의 혼합 기체를 전자식 점화기를 이용하여 900 ~ 1,400℃의 화염 온도를 구현할 수 있도록 설계하였다. 공기공급 온도조건은 35℃를 기준으로 하였으나, 압축공기시스템의 공기 출구 온도가 다르므로 출구 온도에 따라 공기량 및 연료유량을 조정하였다. 연소식 가스버너의 주요 요구 사양은 Table 1과 같다.
Table 1.
Specifications of combustion-type gas burner.
가스버너 연소출력은 완전연소 반응을 가정하여 Eq. 1에 의해 계산하였으며, 연소화염의 속도는 Eq. 2와 같이 연소가스 속도계산식을 통해 계산하였다. Eq. 2에서 적용된 CP_mol은 연료 1 mol이 당량비(Equivalence ratio, Φ)가 고려된 공기와 완전 연소 반응하여 나온 반응물의 mol수이며, Ctemp은 화염 온도 상승에 따른 보정 상수 값이다.
: Fuel flow rate
: Combustion reaction product mol
: Temperature correction constant
연소기 화염 온도와 연소가스 속도는 당량비와 연소출력 제어에 의해 조절하였으며, 먼저 연소출력을 변경하여 연소가스 속도를 조절한 후 당량비로 화염 온도를 조절하였다. 이러한 절차를 몇 차례 반복하여 원하는 조건을 설정할 수 있도록 하였으며, 이후 제어 패널의 자동 로직에 의해 쓰로틀 조절만으로 제어가 될 수 있도록 하였다. 상기 설계에 따라 제작된 버너시스템 단품 시험결과 설계 목표치를 달성하였으며, Fig. 11의 당량비와 연소출력 제어에 의해 Fig. 12와 같이 목표 온도 1,400℃ 화염 온도가 분사노즐에 설치된 온도센서(R type)에 의해 측정되었다.
2.4 제어/DAS 시스템
제어 패널의 전기용량은 380 Vac, 200 kW로서 제어패널과 내마찰 시험장치 구성품에 필요한 전원을 공급할 수 있도록 하였다. RS485 통신 기반 운전 및 속도제어를 통해 로터디스크 구동 모터의 인버터 제어 및 감시를 하였으며, PLC 기반 제어와 TCP/IP 통신 기반으로 구성품의 제어 및 상태를 감시할 수 있도록 하였다. 시스템 제어는 Fig. 13과 같이 버너 시스템(압축공기시스템, 연료공급장치, 밸브 등), 시편 위치 제어부(스텝모터), 냉각시스템(칠러, 밸브 등) 등 각 구성품을 제어할 수 있도록 설계하였다. 단, 화재 또는 비상상황이 발생할 경우를 대비하여 제어 패널이 아닌 별도의 Hot wire로 연결된 비상정지 버튼을 설치하여 버너시스템과 구동모터를 정지할 수 있도록 하였다.
DAS(Data Aquisition System) 시스템은 제어 패널과 통신하여 버너시스템, 구동 모터, 시편위치 등을 제어하고, 온도ㆍ진동ㆍ속도ㆍ힘ㆍ간극을 측정 및 저장하는 기능을 수행하도록 하였다. 또한 고온, 고속회전 환경에서 로터디스크 샤프트를 지지하는 볼베어링부의 손상과 관련하여 온도가 80~90℃를 초과하지 않도록 75℃에서 주의신호를 화면에서 표시할 수 있도록 하였으며, 이외 주요 관심부에 관한 안전주의 기준을 정하여 알람신호를 설정할 수 있도록 하였다.
3. 열전달 해석 및 검증시험 결과
3.1 내마찰 시험장치 열전달 해석결과
고온 내마찰 시험장치의 마모성 세라믹코팅 시편의 표면 온도 범위가 버너시스템이 시험 장치에 체결된 상태에서 1,100~1,150℃수준에 도달할 수 있는지와 연소 화염에 의한 시편 주변 부품의 열적 영향성을 사전 점검하기 위해 열전달 해석을 수행하였다.
해석을 위해 고온의 화염제트는 공기로 모사하였으며, 고속 회전하는 로터디스크에서 커팅블레이드와 시편의 접촉 마찰에 의한 발열량은 1회전당 접촉시간이 매우 짧아 무시하는 것으로 가정하였다. 또한 화염 제트 및 로터디스크 주변공기의 유동은 점성 유동(Viscous flow)으로 가정하였다.
열전달 해석결과 영향이 적을 것으로 판단되는 요소는 해석의 효율성을 위해 일부 형상을 수정 및 제거하여 Fig. 14와 같이 해석 형상을 모델링 하였으며, 고속으로 회전하는 커팅 블레이드의 위치는 시편 기준으로 전단 30도 위치에 있다고 가정하였다.
해석 격자는 유체부분과 고체부분을 모두 포함하였으며, Polyhedra 격자로 구성하였다. 사용된 격자의 수는 Cells(2,886,460ea), Faces(15,472,2 02ea), Nodes(10,340,077ea)로 설정하였다. 로터
디스크의 커팅 블레이드가 이동하는 부분은 해석의 효율성을 위해 회전하는 유동장(Reference Frames, Rotating Frames)으로 설정하였고, 유체 부분은 Rotating Frame을 이용하여 블레이드 회전속도(450 m/s)를 설정하였다.
열전달 해석을 위해 에너지 방정식을 함께 계산하였으며, Viscous model은 SST k- ω를 이용하였다. 수렴도 확인을 위해 입출구의 유속과 주요 부분의 온도 변화를 확인하여 그 값이 거의 변하지 않는 지점을 수렴조건으로 설정하였다.
열전달 해석은 노즐로 유입되는 공기의 전압력이 150 kPa이고, 블레이드 회전속도가 450 m/s 일 때 노즐 입구에서 화염 온도가 1,300℃와 1,400℃의 2가지 조건에서 수행하였다. 해석에서 코팅시편과 커팅 블레이드의 접촉 마찰에 의한 발열을 무시하였기 때문에 실제 온도는 예측 값과 유사하거나 조금 높을 것으로 판단하였다.
해석결과 Table 2와 같이 Inlet flame temperature 1,300℃ 조건에서 화염에 노출된 시편의 최대온도가 1,183℃수준으로 목표하였던 온도 이상으로 조건을 달성함을 확인하였으며, Fig. 15는 화염 노출부와 비노출부에서 온도 분포를 나타낸다.
가스버너에서 토출된 화염에 의한 시험장치 주변 열 영향성은 해석 결과 Fig. 16과 같이 고속으로 회전하는 로터디스크에 의해 유입된 냉각 공기와 함께 화염이 배기 덕트를 통해 배출되어 주변에 미치는 영향이 미비함을 확인하였다.
Table 2.
Temperature estimation value of specimen
no. | Inlet Cond. | Coating Surface temp(℃) | Exit temp | ||
Flame exposed | Flame unexposed | Avg. | |||
1 | 1,400℃ | 1,269.4 | 867.4 | 1,014.5 | 301.7 |
2 | 1,300℃ | 1,183.0 | 811.9 | 947.7 | 290.5 |
3.2 내마찰 시험장치 검증 결과
고온 내마찰 시험과 관련하여 Sporer, D.(2007)는 Fig. 17과 같이 마모성 코팅(Abradable coating)에 대한 Wear map 작성을 위한 표준 시험조건을 통해 시험결과를 제시한 바 있다[6]. 이에 따라 로터디스크의 블레이드 팁 속도가 410 m/s일 때 버너의 연소출력을 조절하여 코팅 시편의 표면온도가 목표온도인 1,100~1,150℃에 도달하는지를 검증해 보았다.
시험 장치는 고온 시험도중에 화염이 장치 밖으로 확산되지 않게 화염가이드를 장착하여 장치 외부에서 Pyrometer를 통한 직접 온도 측정이 어려우며, 시편 근처에 열전대를 장착하고 마모시험을 하면서 측정하기에도 열전대 위치 선정과 안정적인 고정에 문제가 있었다. 따라서 Fig. 18과 같이 코팅 표면온도 보정용 시편을 제작하였으며, 시편 후면에서 R type 센서를 관통하여 표면 근처에 센서 팁을 노출해 온도를 측정하였다.
Fig. 19의 고온 시험결과를 통해 블레이드 팁 속도 410 m/s, 버너 화염온도 약 1,400℃에서 코팅 표면의 온도가 최대 1,114℃에 도달하는 것을 확인하였다. 배기 덕트에서 배출되는 가스온도도 해석결과와 유사하게 300℃이하로 확인되었다.
고온 버너시험 결과이외에도 블레이드 팁 속도 측정시험 결과 목표 속도RPM에서 ±50 rpm 범위에서 제어됨을 확인하였으며, 시편 위치 제어부의 시편 침입율(Incursion rate)은 Table 3과 같이 5 ~ 1,000 ㎛/s에서 2% 이내의 정밀도를 확인할 수 있었다.
4. 결 론
본 연구에서는 터빈입구온도 1,800K급 가스터빈 엔진 개발과 관련하여 고압터빈부의 온도와 로터디스크의 회전속도 환경을 모사하여 슈라우드에 적용되어 평가받고자한 마모성 세라믹코팅(Abradable ceramic coating) 시편의 내마찰 특성을 확인하기 위한 시험 장치를 개발하고자 하였다. 120 kW급 구동모터를 통해 로터디스크를 회전시키면서 목표 속도 250, 350, 410 m/s에서 rpm 기준 ±50 rpm으로 제어되었으며, 시편 위치 제어부는 침입율(Incursion rate) 5~1,000㎛/s에서 약 1% 이내 수준의 정밀도로 제작되었다. 고온 시험을 위해 적용된 연소식 가스버너는 버너 노즐 출구온도 기준 약 1,400℃까지 화염을 발생하였으며, 시험장치 총조립 상태에서 측정한 코팅시편 표면온도 측정시험에서 410 m/s 블레이드 팁 속도 조건의 코팅 표면온도가 최대 1,114℃에 도달하는 것을 확인하였다. 이를 통해 Wear map기준 표준시험 조건에서 마모시험을 수행할 수 있는 시험 장치를 개발되었음을 확인하였다.